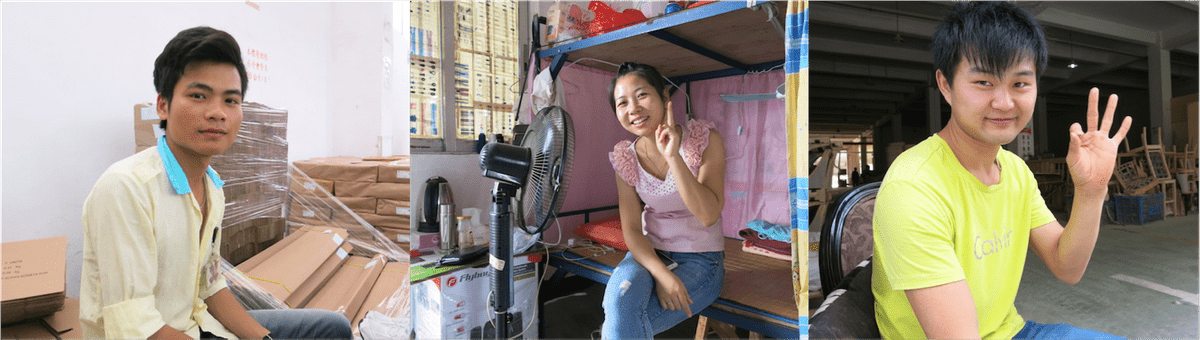
If you are working with small to medium size factories in China you probably encountered many business owners that were formerly employed or even workers in factories. They have been in the field for many years and perpetuate a traditional vision of production and workers management. Whenever you tell them about reducing overtime or giving social benefits there is a high chance they answer to you: “This is China! Workers are all the same, they are just seeking to earn money whatever the conditions”. Truth is this has been the case for many years and still is for quite a lot of migrant workers. However as the new generation, post 1980’s, arrives in the factories it starts to operate a major shift.
“Before joining this factory I was working in an hotel as a manager, I just wanted to try the industry but I do not plan to stay here” (Worker in Zhongshan, 27 y.o.)
Unlike older workers, who sometimes cannot read or write, they are aware of their rights and get more curious about the conditions and benefits offered by their employers. On the top of that they also consider aspects such as their interest in the work, the hardship of the tasks, the working environment and the career evolution. This is not without consequences for the factories, which struggle to retain their workforce and attract workers in peak season.
" The most important in my job? First relationships with my colleagues and the boss, learning skills and then a good salary!" (worker in Xianju, 25 y.o.)”
Yet it might represent a great opportunity for factories to modernize as is brings the question of productivity back in the spotlights. On last decades, unlike in the West, Chinese factories have been relying on an abundant pool of cheap and unqualified workers without trying to optimize the processes. Unfortunately today the low attractiveness of the industry and the high turnover is forcing manufacturers to do more, with fewer workers. Part of the solution lies into improving the efficiency though operation standardization and better production management but another part is about reworking the attractiveness to young workers.
" I got trained to use the new laser cutting machine, older workers don't know how to use it, now I am the only who can that!" (worker in Fuzhou, 29 y.o.)”
Some factories we visited have started to work on this problematic and are going beyond just providing a paycheck to their workers. They propose better canteens and living conditions, various activities after work, better social coverage.
Yet forward thinking factories realized that the key to retain workers does not only lie in financial investments but most importantly in a better human management and providing opportunities in term of training and career.
"I arrived in the factory 18 months ago and recently got promoted: I was trained and now train other people, I am very proud!" (Worker in Zhongshan, 28 y.o.)
Eventhough many factory owners still deny it, generations Y and Z are the future of work and they will have to be reckoned with. They are quickly changing the current paradigm. It now depends on the will of business owners to change their mindset and provide better conditions and fulfillment opportunities for their workers.
